Managing vibration and resonance in hydraulic motors like Linde’s A2FE Series requires careful design considerations and engineering strategies to minimize unwanted oscillations and ensure smooth and stable operation. While I don’t have access to specific details of Linde’s internal processes.
Here are some general approaches they might use to address vibration and resonance in the A2FE Series Motor:
- Balanced Design: Linde may design the A2FE Series Motor with balanced internal components to minimize vibrations caused by uneven forces and motion. This includes optimizing the layout of pistons, cylinders, and valve plates to distribute loads evenly and reduce the occurrence of unbalanced forces.
- Damping Mechanisms: Linde may incorporate damping mechanisms, such as rubber mounts or elastomeric materials, into the design of the A2FE Series Motor to absorb vibrations and dampen resonance frequencies. These damping elements help attenuate vibration energy and prevent it from amplifying and causing structural damage.
- Torsional Analysis: Linde may conduct torsional analysis and modeling of the A2FE Series Motor to identify potential resonance frequencies and modes of vibration. By analyzing the natural frequencies of the motor and its surrounding components, Linde can implement design modifications or tuning adjustments to avoid resonance and minimize vibration levels.
- Precision Manufacturing: Linde ensures tight tolerances and precision manufacturing processes in the production of the A2FE Series Motor to minimize variations in component dimensions and assembly. By maintaining consistent quality and dimensional accuracy, Linde reduces the likelihood of resonance and vibration due to irregularities or mismatches in the motor’s construction.
- Isolation Techniques: Linde may employ isolation techniques to decouple the A2FE Series Motor from external sources of vibration, such as mounting it on vibration-isolating pads or using flexible couplings. These isolation methods help prevent vibration transmission from the motor to the surrounding structure and vice versa, reducing the overall vibration levels.
- Frequency Analysis: Linde may perform frequency analysis and testing on the A2FE Series Motor to identify resonant frequencies and critical vibration modes. By analyzing the frequency response of the motor under different operating conditions, Linde can implement design modifications or control strategies to mitigate resonance and vibration issues.
- Feedback Control Systems: Linde may integrate feedback control systems into the A2FE Series Motor to actively monitor and adjust operating parameters in real-time to suppress vibration and avoid resonance. Closed-loop control algorithms can dynamically adjust motor speed, torque, or displacement to maintain stable operation and minimize vibration levels.
- Field Testing and Validation: Linde conducts extensive field testing and validation of the A2FE Series Motor under various operating conditions to assess its vibration and resonance characteristics in real-world applications. Field data and performance feedback are used to refine the motor design and optimize vibration control strategies for improved reliability and performance.
By implementing these engineering approaches and design strategies, Linde can effectively manage vibration and resonance in their A2FE Series Motor, ensuring smooth and stable operation in a wide range of hydraulic applications.
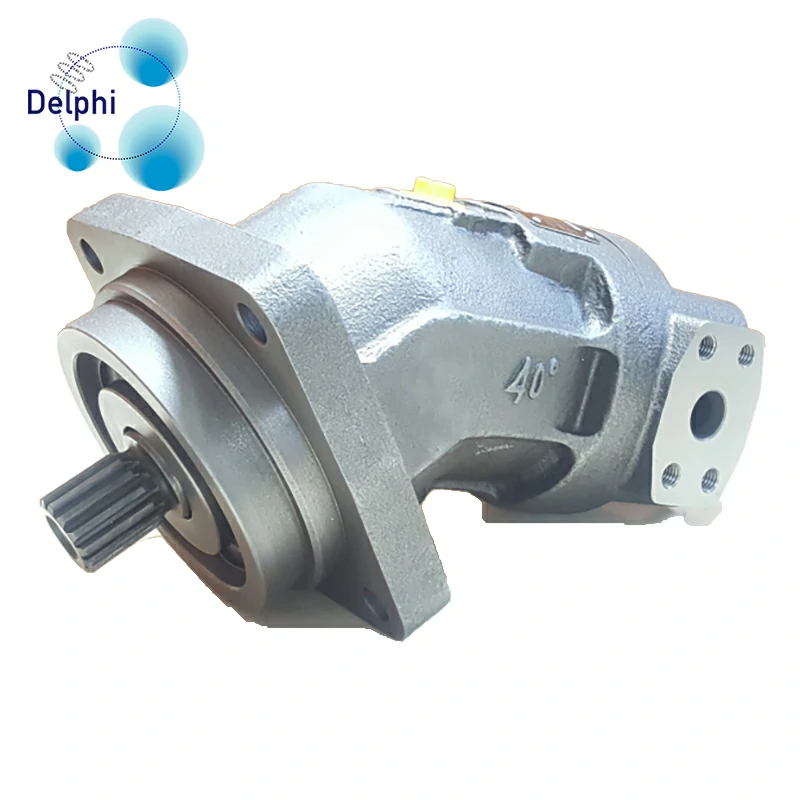