The galvanization process can be adjusted to accommodate different shapes or configurations of metal components, including fittings like 4-way galvanized pipe fittings. The adjustment is made to ensure uniform coating thickness, proper coverage, and optimal adhesion of the zinc coating to various surfaces.
Here’s how the galvanization process is adapted for different shapes or configurations:
- Preparation and Cleaning:
- Regardless of the shape, the metal components undergo thorough cleaning to remove any contaminants, oxides, or scale. This step is crucial for promoting good adhesion of the zinc coating.
- Surface Inspection:
- Different shapes may have varying surface characteristics. Before galvanization, the surfaces are inspected to identify any irregularities or areas that may affect coating uniformity.
- Fluxing:
- The metal components are fluxed to remove any remaining oxides and prepare the surface for galvanization. Fluxing is adjusted based on the specific requirements of different shapes or configurations.
- Material Handling:
- The handling of components with different shapes is optimized to ensure proper immersion and withdrawal from the galvanizing bath. Specialized fixtures or racks may be used to hold components securely during the process.
- Galvanizing Bath Parameters:
- The temperature and composition of the zinc bath are adjusted to accommodate different shapes. The bath parameters are optimized to ensure complete coverage and uniform coating thickness on all surfaces.
- Immersion and Withdrawal Speed:
- The immersion and withdrawal speed of components are adjusted based on their shape and size. This optimization helps achieve the desired coating thickness and uniformity.
- Agitation of the Zinc Bath:
- Agitation of the zinc bath may be adjusted to ensure even distribution of the molten zinc over complex or irregular shapes. 4 way galvanized pipe fitting Proper agitation prevents uneven coating and ensures complete coverage.
- Drying and Cooling:
- The drying and cooling process is adapted to prevent distortion or damage to components with intricate shapes. Controlled cooling rates are employed to solidify the zinc coating uniformly.
- Post-Galvanizing Treatments:
- Depending on the shape and configuration, certain post-galvanizing treatments may be applied. This can include passivation or additional surface treatments to enhance the corrosion resistance of the coating.
- Quality Control Inspection:
- Components with different shapes undergo thorough quality control inspections. This may include visual inspections, coating thickness measurements, and adhesion tests to ensure compliance with specifications.
- Customized Fixtures or Hooks:
- Specialized fixtures or hooks may be designed to hold components securely during galvanization. This ensures that all surfaces are exposed to the zinc bath and that the coating is applied uniformly.
- Masking or Plugging:
- For components with specific areas that should not be coated, masking or plugging techniques may be employed. This prevents zinc from adhering to designated regions, allowing for selective galvanization.
- Adjustment for Hollow Sections:
- Special considerations are made for hollow sections or components with internal spaces. Techniques such as centrifuging or venting may be used to ensure proper coating inside these areas.
- Continuous Process Monitoring:
- Continuous monitoring of the galvanization process is essential. This may involve real-time adjustments based on feedback from sensors or inspection systems to address variations in shape and configuration.
By customizing various parameters and processes based on the specific shapes or configurations of metal components, manufacturers can ensure that the galvanization process effectively protects the entire surface of the components, regardless of their geometry. This adaptability is crucial for achieving consistent and high-quality coatings on a wide range of products.
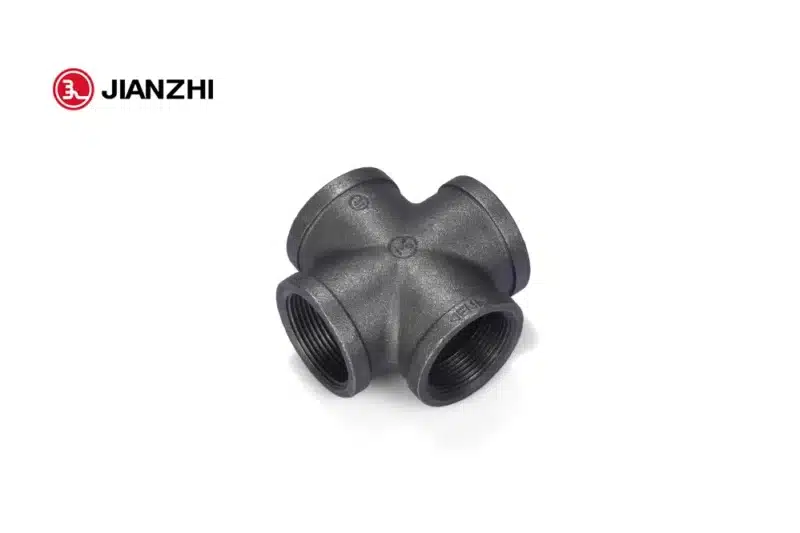