Introduction
Dispensing peristaltic pumps have revolutionized the field of fluid transfer and dispensing, offering precise and reliable solutions across various industries. These pumps utilize the unique peristaltic action, which involves the compression and relaxation of a flexible tube, to propel fluids without any contact between the fluid and the pump components. In this article, we explore the capabilities and applications of dispensing peristaltic pumps, highlighting their advantages and the industries they serve.
How Dispensing Peristaltic Pumps Work
Dispensing peristaltic pumps operate based on a simple yet efficient mechanism. The pump consists of a flexible tube or hose and a rotating roller assembly. As the rollers rotate, they compress the tube against a fixed housing or track, creating a series of sealed cavities. This compression propels the fluid within the tube, allowing for precise and controlled dispensing. The absence of direct contact between the fluid and the pump components ensures superior hygiene, eliminates the risk of contamination, and enables easy cleanup and maintenance.
Advantages of Dispensing Peristaltic Pumps
- a. Precise Fluid Control: Dispensing peristaltic pumps offer exceptional accuracy and repeatability in fluid dispensing applications. The controlled compression of the flexible tube allows for precise volume control, ensuring consistent dispensing and minimizing wastage.
- b. Gentle Fluid Handling: The peristaltic action of these pumps ensures gentle fluid handling, making them ideal for sensitive liquids or delicate substances that should not be exposed to excessive shear or agitation. This feature is particularly valuable in pharmaceutical, biotechnology, and food industries where product integrity is paramount.
- c. Wide Range of Fluid Compatibility: Dispensing peristaltic pumps are compatible with a broad range of fluids, including corrosive chemicals, viscous solutions, abrasive slurries, and even shear-sensitive materials. The use of different tube materials and sizes allows for versatility in accommodating various fluid types.
- d. Easy Maintenance and Cleaning: Since the fluid only comes into contact with the tube, the pump components remain clean and protected. This feature simplifies maintenance procedures, reduces downtime, and minimizes the risk of cross-contamination. Additionally, the tubing can be easily replaced, ensuring quick and cost-effective maintenance.
Applications of Dispensing Peristaltic Pumps
- a. Pharmaceutical and Biotechnology: Dispensing peristaltic pumps play a crucial role in pharmaceutical manufacturing, where precise and sterile fluid transfer is essential. They are widely used in processes such as liquid dispensing, filling vials or syringes, media and buffer transfer, and bioreactor feeding. The ability to maintain sterility and accurately dispense small volumes makes these pumps indispensable in this industry.
- b. Laboratory and Research: In laboratory settings, dispensing peristaltic pumps find application in sample preparation, reagent dispensing, cell culture media handling, and chromatography systems. Their accuracy, ease of use, and contamination-free operation make them reliable tools in research and analytical laboratories.
- c. Food and Beverage: Dispensing peristaltic pumps are utilized in the food and beverage industry for precise filling of bottles, containers, and packaging. They are commonly employed in processes involving flavorings, additives, sauces, and dairy products. The hygienic operation and ability to handle particulates or delicate ingredients make them ideal for maintaining product quality.
- d. Industrial and Manufacturing: Dispensing peristaltic pumps are employed in various industrial applications, including chemical dosing, adhesive dispensing, inkjet printing, and paint or coating application. Their accuracy and versatility make them valuable tools for consistent and controlled dispensing in manufacturing processes.
What are the main factors to consider when choosing a dispensing peristaltic pump?
When choosing a dispensing peristaltic pump, several factors should be considered to ensure the optimal selection for your specific application. Here are the main factors to keep in mind:
- Fluid Compatibility: Assess the compatibility of the pump materials with the fluid being dispensed. Consider the chemical composition, viscosity, and temperature of the fluid. Choose a pump that can handle the specific characteristics of your fluid without causing degradation, clogging, or tube failure.
- Flow Rate and Dispensing Accuracy: Determine the required flow rate and precision for your application. Consider the desired dispensing volume, accuracy, and repeatability. Different pumps have varying flow rate capabilities, and some models offer adjustable speed and control options to meet specific requirements.
- Tube Selection: The tube material and size play a crucial role in the pump’s performance and compatibility with the fluid. Consider the chemical resistance, flexibility, and durability of the tube material. Additionally, select the appropriate tube size to match the desired flow rate and prevent excessive tubing wear.
- Pressure Requirements: Evaluate the system pressure needed for your application. Ensure that the selected pump can generate the required pressure to dispense the fluid effectively, considering any potential backpressure or resistance in the system.
- Ease of Maintenance and Tube Replacement: Consider the ease of maintenance and tube replacement. Opt for a pump that allows quick and convenient tube changes, reducing downtime and maintenance costs. Some pumps feature tool-free tube replacement mechanisms for efficient and hassle-free maintenance.
- Sterility and Hygiene: In applications where sterility is critical, such as pharmaceutical or biotechnology processes, choose a pump with sanitary and cleanable components. Look for pumps with smooth surfaces, easy disassembly for cleaning, and options for sterile tubing connections.
- Control and Automation: Assess whether you require advanced control and automation features. Some pumps offer programmable dispensing parameters, digital displays, and integration with external control systems. These features can enhance precision, repeatability, and ease of use.
- Cost and Value: Consider the overall cost and value of the pump. Evaluate the initial investment, maintenance costs, and the expected lifespan of the pump. It’s important to strike a balance between cost-effectiveness and the required performance for your application.
- Support and Service: Research the reputation and reliability of the pump manufacturer. Ensure they provide adequate technical support, documentation, and warranty coverage. A reputable manufacturer will offer assistance and guidance throughout the pump’s lifespan.
Conclusion
Dispensing peristaltic pumps offer an efficient and reliable solution for precise fluid transfer and dispensing across multiple industries. Their unique peristaltic action, hygienic operation, and compatibility with a wide range of fluids make them an indispensable tool for achieving accurate and controlled dispensing in diverse applications. As technology continues to advance, these pumps are likely to further expand their capabilities and find new applications, driving innovation and efficiency in fluid handling processes.
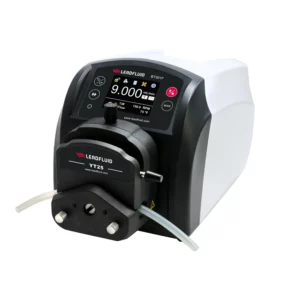